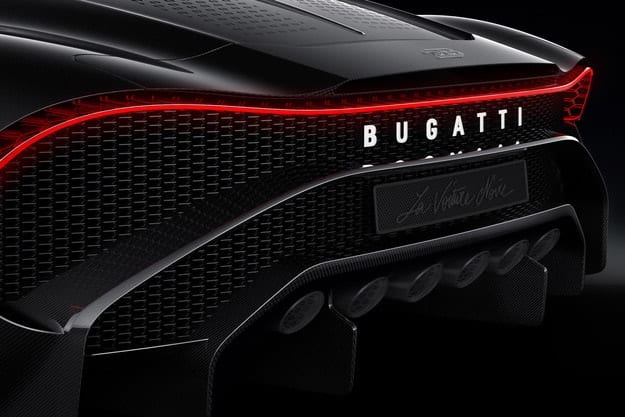
Bugatti: imprimarea 3D în inima Chironului
Producătorul francez folosește această tehnologie în 2018 pentru modelul Chiron Sport.
Din 2018, producătorul pe bază de Molsheim folosește tehnologia de imprimare 3D pentru fabricarea anumitor piese hipersport Chiron, cum ar fi vârfurile de evacuare din titan ale modelelor Pur Sport și Super Sport 300+.
La fel ca Ettore Bugatti, fondatorul mărcii tricolore care prezintă în mod regulat inovații în designul modelelor sale (îi datorăm în principal jantele din aliaj și puntea față goală), inginerii responsabili de dezvoltarea noilor modele Bugatti includ ultimele inovații. în construcții sau inginerie în creațiile sale. Tehnologia de imprimare 3D, ale cărei avantaje sunt deja bine cunoscute, este una dintre ele.
Bugatti a folosit această tehnologie în 2018 în Chiron Sport, care a fost apoi echipat cu vârfuri de evacuare fabricate din Inconel 718, un aliaj dur și ușor de nichel-crom deosebit de rezistent la căldură (în acest caz, aluminiul se topește). Următoarele modele ale mărcii (Divo, La Voiture Noire, Centodieci ...) vor beneficia, de asemenea, de acest proces de fabricație pentru țevile de evacuare.
Aceste elemente tipărite 3D au mai multe avantaje. Pe de o parte, sunt mai rezistente la căldură și elimină acumularea de căldură creată de motorul de 8,0 litri W16 1500 CP și sunt, de asemenea, mai ușoare decât injectoarele convenționale. (Chiron Sport cântărește doar 2,2 kg, de exemplu cu 800 g mai puțin decât un injector convențional).
În cazul noului Chiron Pur Sport, Bugatti produce duze de evacuare din titan imprimate 3D, iar producătorul indică faptul că aceasta este „prima piesă metalică vizibilă tipărită în 3D cu omologare a traficului rutier”. Acest accesoriu are 22 cm lungime și 48 cm lățime și cântărește doar 1,85 kg (inclusiv grătar și întreținere), ceea ce este cu aproximativ 1,2 kg mai puțin decât „standardul” Chiron.
Un sistem special de imprimare cu laser utilizat pentru imprimarea 3D constă din unul sau mai multe lasere, care la rândul lor topesc straturi de praf între 3 și 4 microni. 4200 de straturi de pulbere metalică se adună unul peste celălalt și se fuzionează împreună pentru a forma duza de ieșire Chiron Pur Sport care va rezista la temperaturi de peste 650 de grade Celsius, oferind în același timp izolație termică părților adiacente datorită peretelui exterior dublu.
Aceste elemente vor fi în cele din urmă acoperite special înainte de a fi inspectate cu atenție și instalate pe vehicul. De exemplu, Chiron Sport este șlefuit cu corindon și lăcuit în negru cu vopsea ceramică la temperaturi ridicate, în timp ce Chiron Pur Sport și Super Sport 300+ sunt disponibile într-un finisaj mat din titan.
Prin garantarea durabilității, ultra-ușurinței și esteticii pieselor, tehnologia de imprimare 3D, utilizată până acum în principal în aeronautică și spațiu, pare să-și fi găsit în sfârșit locul printre producătorii de automobile, chiar și cei mai pretențioși.
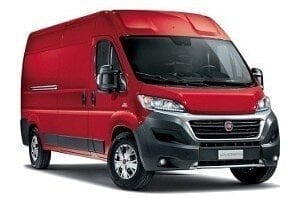
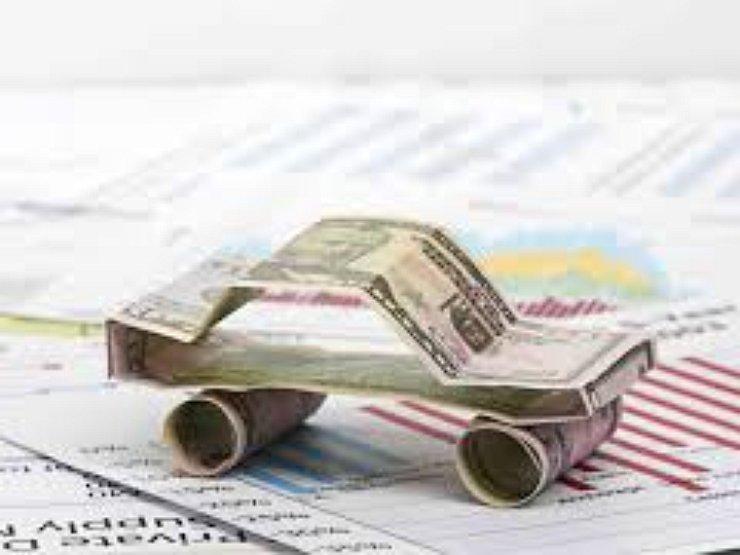