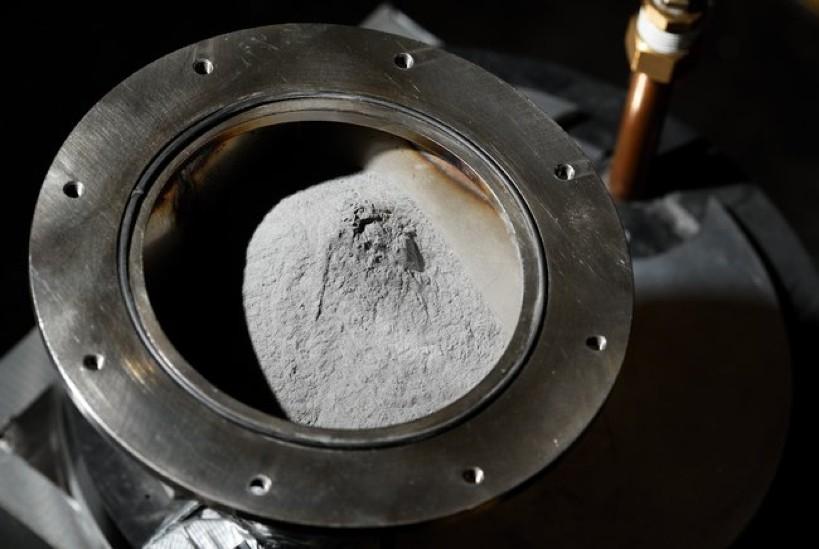
Viitorul în pulbere
Compania suedeză VBN Components produce produse din oțel folosind tehnologii aditive folosind pulbere cu aditivi, în principal unelte precum burghie și freze. Tehnologia de imprimare 3D elimină nevoia de forjare și prelucrare, reduce consumul de materii prime și oferă utilizatorilor finali o gamă mai largă de materiale de înaltă calitate.
Oferta componentelor VBN include de ex. Vibenite 290care, conform companiei suedeze, este cel mai dur oțel din lume (72 HRC). Procesul de creare a Vibenite 290 este de a crește treptat duritatea materialelor până la. Odată ce piesele dorite sunt imprimate din această materie primă, nu este necesară nicio prelucrare ulterioară, în afară de măcinare sau EDM. Nu necesită tăiere, frezare sau găurire. Astfel, compania realizează piese cu dimensiuni de până la 200 x 200 x 380 mm, a căror geometrie nu poate fi produsă folosind alte tehnologii de fabricație.
Oțelul nu este întotdeauna necesar. O echipă de cercetare de la HRL Laboratories a dezvoltat o soluție de imprimare 3D. aliaje de aluminiu cu rezistență mare. Se numeste metoda nanofuncțională. Mai simplu spus, noua tehnică constă în aplicarea unor pulberi nanofuncționale speciale pe o imprimantă 3D, care sunt apoi „sinterizate” cu un laser în straturi subțiri, ceea ce duce la creșterea unui obiect tridimensional. În timpul topirii și solidificării, structurile rezultate nu sunt distruse și își păstrează întreaga rezistență datorită nanoparticulelor care acționează ca centre de nucleare pentru microstructura dorită a aliajului.
Aliajele de înaltă rezistență, cum ar fi aluminiul, sunt utilizate pe scară largă în industria grea, tehnologia aviației (de exemplu, fuselaj) și piesele auto. Noua tehnologie de nanofuncționalizare le oferă nu numai rezistență ridicată, ci și o varietate de forme și dimensiuni.
Adunare în loc de scădere
În metodele tradiționale de prelucrare a metalelor, deșeurile sunt îndepărtate prin prelucrare. Procesul aditiv funcționează invers - constă în aplicarea și adăugarea de straturi succesive dintr-o cantitate mică de material, creând piese XNUMXD de aproape orice formă pe baza unui model digital.
Deși această tehnică este deja utilizată pe scară largă atât pentru prototipare, cât și pentru turnarea modelelor, utilizarea ei directă în producția de bunuri sau dispozitive destinate pieței a fost dificilă din cauza eficienței scăzute și a proprietăților nesatisfăcătoare ale materialului. Cu toate acestea, această situație se schimbă treptat datorită muncii cercetătorilor din multe centre din întreaga lume.
Prin experimente minuțioase, cele două tehnologii principale de imprimare XNUMXD au fost îmbunătățite: depunerea cu laser a metalului (LMD) i topire selectivă cu laser (ULM). Tehnologia laser face posibilă crearea cu precizie a detaliilor fine și obținerea unei calități bune a suprafeței, ceea ce nu este posibil cu imprimarea cu fascicul de electroni 50D (EBM). În SLM, vârful fasciculului laser este îndreptat spre pulberea materialului, sudându-l local conform unui model dat, cu o precizie de 250 până la 3 microni. La rândul său, LMD folosește un laser pentru a procesa pulberea pentru a crea structuri XNUMXD autoportante.
Aceste metode s-au dovedit a fi foarte promițătoare pentru crearea de piese de aeronave. și, în special, depunerea cu laser a metalului extinde posibilitățile de proiectare pentru componentele aerospațiale. Ele pot fi realizate din materiale cu structuri interne complexe și gradienți care nu erau posibil în trecut. În plus, ambele tehnologii laser fac posibilă crearea de produse cu geometrie complexă și obținerea unei funcționalități extinse a produselor dintr-o gamă largă de aliaje.
În septembrie anul trecut, Airbus a anunțat că și-a echipat producția A350 XWB cu imprimare aditivă. suport de titan, fabricat de Arconic. Acesta nu este sfârșitul, deoarece contractul Arconic cu Airbus prevede imprimarea 3D din pulbere de titan-nichel. parti ale corpului i sistem de propulsie. Cu toate acestea, trebuie remarcat faptul că Arconic nu folosește tehnologia laser, ci propria versiune îmbunătățită a arcului electronic EBM.
Unul dintre reperele în dezvoltarea tehnologiilor aditive în prelucrarea metalelor va fi probabil primul prototip prezentat la sediul grupului olandez Damen Shipyards Group în toamna anului 2017. elicea navei aliaj metalic numit după VAAMpeller. După teste corespunzătoare, dintre care majoritatea au avut deja loc, modelul are șansa de a fi aprobat pentru utilizare la bordul navelor.
Întrucât viitorul tehnologiei de prelucrare a metalelor constă în pulberile din oțel inoxidabil sau componentele din aliaje, merită să cunoașteți principalii jucători de pe această piață. Potrivit „Additive Manufacturing Metal Powder Market Report” publicat în noiembrie 2017, cei mai importanți producători de pulberi metalice de imprimare 3D sunt: GKN, Hitachi Chemical, Rio Tinto, ATI Powder Metals, Praxair, Arconic, Sandvik AB, Renishaw, Höganäs AB. , Metaldyne Performance Group, BÖHLER Edelstahl, Carpenter Technology Corporation, Aubert & Duval.
Elice imprimare WAAMpeller
Faza lichida
Cele mai cunoscute tehnologii de aditivi metalici se bazează în prezent pe utilizarea pulberilor (așa se creează vibenita menționată mai sus) „sinterizate” și topite cu laser la temperaturile ridicate necesare pentru materia primă. Cu toate acestea, apar noi concepte. Cercetătorii de la Laboratorul de Inginerie Criobiomedicală al Academiei Chineze de Științe din Beijing au dezvoltat o metodă Imprimare 3D cu „cerneală”, constând dintr-un aliaj metalic cu un punct de topire puțin peste temperatura camerei. Într-un studiu publicat în revista Science China Technological Sciences, cercetătorii Liu Jing și Wang Lei demonstrează o tehnică de imprimare în fază lichidă a aliajelor pe bază de galiu, bismut sau indiu cu adăugarea de nanoparticule.
În comparație cu metodele tradiționale de prototipare a metalelor, imprimarea 3D în fază lichidă are câteva avantaje importante. În primul rând, se poate obține o rată relativ mare de fabricare a structurilor tridimensionale. În plus, aici puteți regla mai flexibil temperatura și debitul lichidului de răcire. În plus, metalul conductor lichid poate fi utilizat în combinație cu materiale nemetalice (cum ar fi materialele plastice), ceea ce extinde posibilitățile de proiectare pentru componente complexe.
Oamenii de știință de la Universitatea American Northwestern au dezvoltat, de asemenea, o nouă tehnică de imprimare 3D din metal, care este mai ieftină și mai puțin complexă decât se știa anterior. În loc de pulbere metalică, lasere sau fascicule de electroni, folosește cuptor conventional i material lichid. În plus, metoda funcționează bine pentru o mare varietate de metale, aliaje, compuși și oxizi. Acesta este similar cu etanșarea duzei pe care o cunoaștem cu materialele plastice. „Cerneala” constă dintr-o pulbere metalică dizolvată într-o substanță specială cu adăugarea unui elastomer. In momentul aplicarii este la temperatura camerei. După aceea, stratul de material aplicat din duză este sinterizat cu straturile anterioare la o temperatură ridicată creată în cuptor. Tehnica este descrisă în revista de specialitate Advanced Functional Materials.
Metoda chineză de imprimare în fază de metal lichid
În 2016, cercetătorii de la Harvard au introdus o altă metodă care poate crea structuri metalice XNUMXD. tipărit „în aer”. Universitatea Harvard a creat o imprimantă 3D care, spre deosebire de altele, nu creează obiecte strat cu strat, ci creează structuri complexe „în aer” – din metal înghețat instantaneu. Dispozitivul, dezvoltat la Școala de Inginerie și Științe Aplicate John A. Paulson, imprimă obiecte folosind nanoparticule de argint. Laserul focalizat încălzește materialul și îl topește, creând diverse structuri, cum ar fi o spirală.
Cererea de pe piață pentru produse de consum imprimate 3D de înaltă precizie, cum ar fi implanturi medicale și piese de motoare de aeronave, crește rapid. Și pentru că datele despre produse pot fi partajate cu alții, companiile din întreaga lume, dacă au acces la pulbere metalică și la imprimanta 3D potrivită, pot lucra pentru a reduce costurile de logistică și de inventar. După cum știți, tehnologiile descrise facilitează foarte mult fabricarea pieselor metalice cu geometrie complexă, înaintea tehnologiilor tradiționale de producție. Dezvoltarea de aplicații specializate va duce probabil la prețuri mai mici și la deschiderea către utilizarea imprimării 3D și în aplicațiile convenționale.
Cel mai dur oțel suedez - pentru imprimare 3D:
Cel mai dur oțel din lume - fabricat în Uppsala, Suedia
Film de aluminiu pentru imprimare:
Revoluție în metalurgie: imprimare 3D a aluminiului de înaltă rezistență

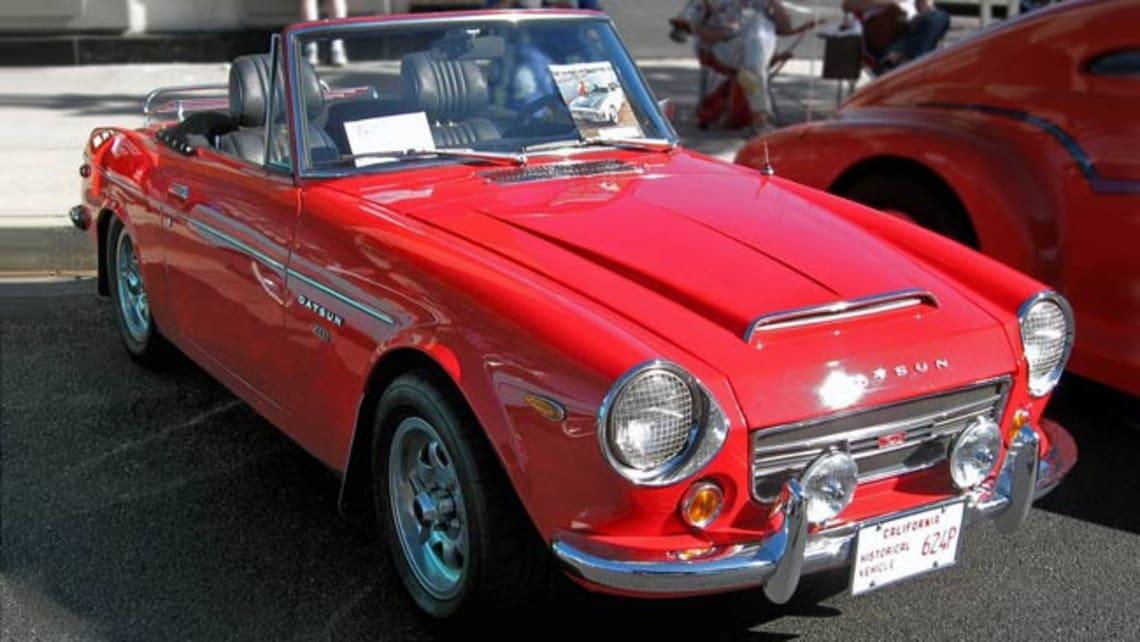
Un comentariu
Anonim
Amuzant